The lever arm was replaced by the telescopic shock absorber in the 1960s. This was driven by improved road and highway conditions, higher average speeds, and drivers’ expectations for better handling. Telescopic shock absorbers are more efficient at dissipating heat due to their larger volume of working fluid and higher surface area to fluid volume ratio. The only area where lever-arm shock absorbers are still actively used is in tank suspensions, where the compact size and unique geometry of the lever-arm shock absorbers allow them to be easily integrated with the torsion bars of the suspension, while the massive tank chassis acts as a huge radiator, alleviating the heat dissipation problem. Some designs of this shock absorber are well suited for conversion into active suspension actuators, and at least one modern main battle tank (the Russian T-14 Armata) is said to have such a suspension.
The lever-arm shock absorber was the first hydraulic shock absorber or damper used in automotive suspensions. They appeared in the 1930s and were most commonly used in the 1950s and 1960s, but were replaced by telescopic shock absorbers in the 1970s. One of the earliest patents for hydraulic lever arm shock absorbers was granted in 1925 to Georges de Ram, who was already a well-known manufacturer of friction disc shock absorbers. In 1930, Ralph Piot invented the hydraulic shock absorber as a development to replace the previous friction discs. Friction discs, at best, provide a constant damping force, regardless of the size or speed of the suspension movement. Using the viscous device of hydraulic oil, the resistance increases with speed, thus providing better damping for larger suspension bumps.
They were first developed by Maurice Houdaille around 1906, but were neglected for many years in favor of simpler friction devices. One hydraulic shock absorber is the rotary vane type, the so-called Houdaille shock absorber. They consist of a cylindrical, oil-filled body that is bolted to the chassis. The lever arm is attached to the axle, and inside the cylinder, it turns a spindle with a vane or paddle. The vane has only a small hole in it through which the hydraulic oil can pass. The resistance to flow through the small hole provides the damping effect.
This type was most common before the war, but Ferrari continued to use Houdaille vanes on its F1 cars until the late 1950s.
Derived from a patent filed by Georges de Ram in 1925 for a hydraulic lever-arm shock absorber. Georges de Ram patented the design for a hydraulic lever-arm shock absorber in 1925, which was further developed after the war. This type of shock absorber has a large cast body containing a cylinder and piston connected to a similar spindle and lever arm. Some use a pair of pistons for impact and rebound, others use a double-acting piston. Some, such as the Volkswagen Beetle before 1949-1951, are equipped with single-acting shock absorbers only, without rebound damping. The flow of hydraulic oil around the piston is carried out by valves mounted in the body. Separate valves are provided for each direction, with the useful feature of different impact and rebound resistance. These valves are sometimes easily adjustable from the outside of the shock absorber body.
Front suspension with lever arm shock absorbers forming the upper wishbones. Many cars of this period began to use independent front suspension, usually double wishbones. The upper wishbones also conveniently served as the levers for the shock absorbers, thus reducing the mass and volume of the suspension and avoiding the use of at least one ball joint. The main axis of the shock absorbers now became the upper suspension pivot, which was usually double ended. One of the last production sports cars still using lever arm shock absorbers was the MG B. This car had lever arm shock absorbers in the upper wishbones. A later popular handling upgrade was to switch to telescopic shock absorbers. The lever arm wishbones still remained, but were now a simple wishbone with no damping.
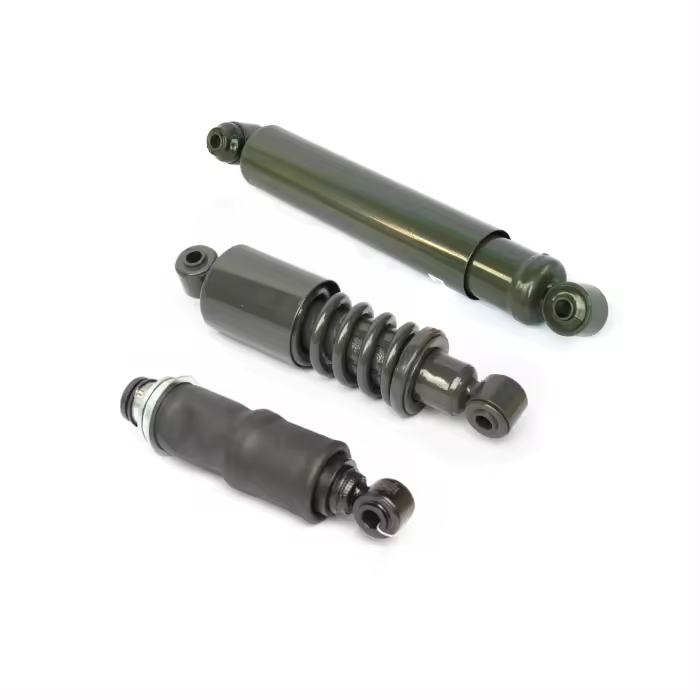